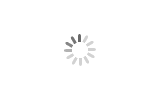
- Gaea
- China
Gaea O2 rock blasting technology is an upgraded technology based on CO2 rock blasting technology. This technology overcomes the disadvantage that CO2 rock blasting system cannot be exported. In terms of use effect, it is more powerful and safer. This technology has been widely used in many Southeast Asian and South American countries. It is a patented technology of Gaea.
Gaea O2 gas Energy Rock Splitting system CO2 rock blasting system rock demolition
Technical Background:
The technology in which liquid oxygen is absorbed into solid combustibles is called "liquid oxygen rock blasting system"
The explosive power and intensity of the liquid oxygen rock blasting system far exceeds that of current mining explosives (50~150%); its price is only a quarter of that of ammonium nitrate explosives; and in China, after liberation, After a certain mine switched to a new loading operation method, no accident occurred within 4 to 5 years.
Based on the above facts, liquid oxygen explosives can become the safest and most economical explosives with the highest explosive power by taking necessary safety measures or changing the old installation methods.
O2 rock blasting technology is an upgrade of Gaea's CO2 rock blasting technology. In the past, due to the presence of a chemical in CO2 rock blasting technology, this technology could not be exported. Based on this background, Gaea developed O2 rock blasting technology, which is safer and easier to operate.The blasting cost is about $1 per m³
In summary, the embodiments of the utility model provide a gas expansion device in a hole, which has at least the following advantages or beneficial effects:
The utility model uses liquid oxygen as a gas expansion agent, which is environmentally friendly and pollution-free; high-purity oxygen assists combustion, and a small amount of sparks can cause the gas to expand rapidly to form an explosion, without the need to load a large amount of explosives, and has low pollution; the expansion device does not need to be filled with liquid oxygen in advance, and when the expansion device is installed in the blasting hole, it can be filled and exploded immediately, greatly improving the safety of production and transportation; the exterior is made of plastic or glass, and there is no need to use a steel structure, which reduces the blasting cost. Using an aluminum tube as an inflation tube can play a certain supporting role for the exterior of the soft plastic material. At the same time, the aluminum tube also has a certain flexibility, which increases the applicability of the blasting hole and reduces the drilling requirements. Using soft plastic to replace the exterior, soft plastic is easy to be damaged during ignition. When a dud occurs, liquid oxygen will quickly evaporate from the damaged part and the exhaust pipe to the outside air, reducing safety hazards.
Technical principle:
The performance of liquid oxygen rock blasting system varies according to its absorbent type. The absorbents used in liquid oxygen rock blasting systems include: carbon black, soot, charcoal, peat, coal powder, peat, wood (powder), grass (rice, wheat, tall trees, etc.), leather, reed, feather grass , wheat husks, moss, flowers, waste, etc. Absorbents are divided into two types according to chemical properties: carbon and fiber; according to structure, they are divided into two types: powder and strips.
The chemical reaction when the paper tube absorbent explodes is: C+O2→CO2+94 kcal/gram.
In addition to C, the nutrient absorbent contains xenon, which reacts with oxygen and oxidizes to form water:
H2 +½O2 ->H20+58 kcal/mole
Theoretically, the detonation heat of the liquid oxygen rock blasting system is the largest, because it does not contain nitrogen, and nitrogen exists in the explosive as nitro (NO2), which can reduce The release of "energy" when explosives explode. Furthermore, nitrogen is inert in explosive reactions, so that it is of no use in increasing the energy of the explosion. Not only that, when there is too much nitrogen in the explosive, it is easy to generate nitrogen oxide. The generation of ammonia oxide is an endothermic reaction (26 kcal/mole), which also reduces the generation of heat energy during the explosion.
System Composition:
paper splitting tube(Consumables)
Rock splitting tube is composed of special paper tube and some accessories. The internal structure is complex, which effectively ensures the safety of use. The diameter of the paper tube is designed according to the diameter of rock drilling bits, and the longest diameter used is 90mm. The conventional hole diameter ranges from 60-150mm. The length of the paper tube is customized according to customer needs, and the conventional length of the paper tube is 2-15M.
warehouse video show:
2.O2 filling tank(Recycling)
Used to fill liquid oxygen into paper tubes. The conventional capacity is 500kg. 1ton and 2ton gas filling tanks can also be customized. Usually 6kg of liquid oxygen is filled into a 1M splitting tube.
3.Air booster (optional)
The pressure of liquid oxygen reloading can be increased to make the blasting effect better.
Loading:
Refer to our loading chart. We have experience in exporting to many countries and have set up agents in many Southeast Asian and South American countries.
Practical steps:
1.Drilling hole:
2.Insert the rock splitting tube into the hole
3.Use the connecting pipe to connect the gas filling tank and the rock splitting tube
4.Fill the paper tube with liquid Q2
5.Fill the hole with clay
6.Arrange staff to maintain a safe distance
7.Start the launcher and complete the blasting
Complete operation video:
Storage and transportation:
1.The storage temperature should be less than 50°C, and the relative humidityshould be less than 70%, and it should be protected from moisture.
2. During storage and transportation, avoid extrusion, fluorescent lamps, sunlight,ultraviolet radiation and other radiation.
3. Keep away from high pressure, high heat and open flame.
4. The transport vehicle should be equipped with corresponding types and quantitiesof fire-fighting equipment and leakage emergency treatment equipment.
Product advantages:
The liquid oxygen blasting construction scheme is a commonly used blasting technology. It uses liquid oxygen as an oxidant and mixes it with fuel for blasting operations. The liquid oxygen blasting construction scheme has the following advantages:
1.High efficiency: Liquid oxygen is an efficient oxidant that can provide sufficient oxygen supply, making blasting operations faster and more efficient.
2.Safety: The liquid oxygen blasting construction scheme has higher safety than other blasting technologies. Liquid oxygen is in a liquid state at room temperature, not easy to leak and burn, reducing the risk of accidents.
3.Environmental protection: The liquid oxygen blasting construction scheme has less impact on the environment than traditional blasting technologies. Liquid oxygen mainly produces water and carbon dioxide after combustion, and no harmful gases and pollutants are produced.
4.Accuracy: The liquid oxygen blasting construction scheme can be adjusted according to specific engineering needs to control the intensity and range of the blasting and improve the accuracy of the blasting.
5.Applicability: The liquid oxygen blasting construction scheme is suitable for various types of projects, including building demolition, mining, tunnel engineering, etc. It can cope with various complex geological conditions and engineering requirements. Powerful blasting force: Liquid oxygen blasting construction scheme can produce high-energy explosions, which can effectively destroy and demolish hard materials such as rocks, concrete, etc. This makes it advantageous in some projects that require strong blasting force.
6.Flexibility: Liquid oxygen blasting construction scheme can be adjusted and optimized according to specific project needs. Different blasting effects and control ranges can be achieved by changing the ratio of liquid oxygen and fuel, the design of the blasting device, etc.
7.Economical: Liquid oxygen blasting construction scheme is relatively low in cost compared to other blasting technologies. Liquid oxygen as an oxidizer is relatively cheap, and material waste can be reduced through reasonable design and use.
Quality Articles
What is O2 Rock Blasting Technology System?
https://www.stonedemolition.com/news/what-is-o2-rock-blasting-technology-system
Common Problems When Using the O2 Rock Blasting System and How to Overcome Them
How Does the O2 Rock Breaking System technology Work?
https://www.stonedemolition.com/news/how-does-the-o2-rock-breaking-system-technology-work
How Much Can You Make Blasting? A Cost Breakdown of O2 Rock Blasting vs. Traditional Methods
O2 Rock Blasting System Technology: Transforming Real-World Rock Breaking Applications
Liquid Oxygen Rock Blasting System Compared with Traditional Explosive
Liquid Oxygen Rock Blasting System in Quarry Applications
https://www.stonedemolition.com/news/liquid-oxygen-rock-blasting-system-in-quarry-applications
CO2 Rock Blasting System Technology vs. O2 Rock Blasting System Technology
Revolutionizing the Mineral industry: The Impact of Liquid Oxygen Rock Blasting Systems
What Explosive is Used in Rock Blasting? The Growing Role of O2 Rock Blasting
What Materials Are Used in Rock Blasting? The Rising Star of O2 Rock Blasting